Since 2023, the new energy market has entered a new supply and demand cycle, with production capacity accelerating and demand growth slowing down.
Sheng Jianming, Chairman of ZhiJiaNeng, stated at the 2023 High-Tech Lithium Battery Conference that under the risk of periodic oversupply, the elimination race in different segments of the lithium battery industry has already started. However, the new energy industry is a long-term major track, and its long-term development trend will not change due to periodic fluctuations. High-quality production capacity will never be in surplus, and leading companies in niche markets will continue to strengthen. As he mentioned, the Matthew effect in the power battery industry is further intensified. Data shows that from January to October, the installation volume of power batteries by the top 10 battery manufacturers accounted for 97.3%, compared to 95% market share in 2022, an increase of 2.3%.
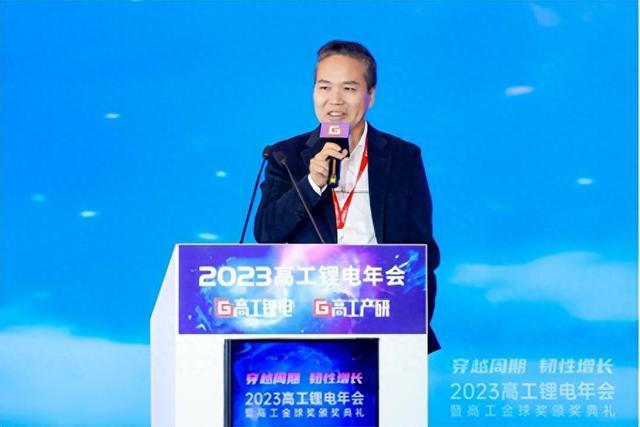
In this process, leading battery companies continue to expand and solidify their advantages established through brand, capital, scale, technology, and channels. This also drives the market concentration of advantageous companies in materials, equipment, and other segments to become increasingly higher.
As a provider of comprehensive solutions for lithium battery manufacturing downstream, ZhiJiaNeng continuously improves its self-research and production rate, and through technological iteration and optimization of mature products, binds top battery customers, from the domestic market to overseas markets, to create high-quality production capacity with stable efficiency and cost advantages for customers.
Sheng Jianming emphasized that ZhiJiaNeng will continue to invest in R&D in the new energy field, extend its industrial layout, iterate technology continuously, actively promote a globalization strategy, and grow in sync with the industry.
At the conference, ZhiJiaNeng director and partner Jiang Peiliang delivered a keynote speech titled “Upgrading Lithium Battery Smart Manufacturing and Reducing Costs and Increasing Efficiency,” detailing ZhiJiaNeng’s new solutions for cost reduction and quality improvement in the new energy field during the intense competition phase of lithium batteries.
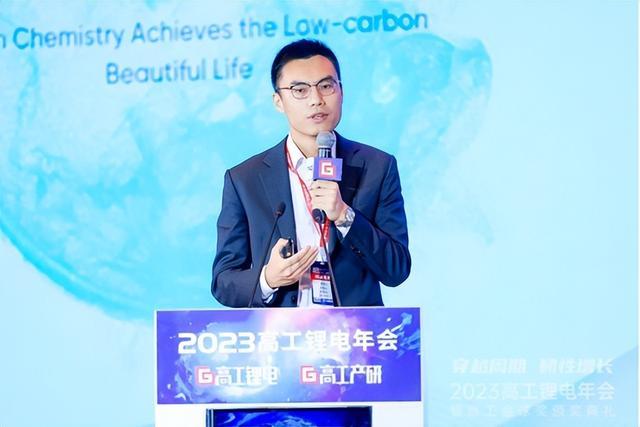
Advanced Formation and Grading Solutions: A Single Production Line Saves 8 Million Yuan in Electricity Costs Per Year
“To secure a ticket to the new segment of the new energy race, for equipment companies, it involves three aspects: reducing the cost of the equipment itself, reducing the investment cost of the production line, and enabling long-term cost reduction in battery production and operation,” Jiang Peiliang stated.
ZhiJiaNeng, with over 20 years of experience in the field of intelligent manufacturing equipment, specializes in lithium battery post-processing formation and grading solutions, lithium battery full-line warehousing and logistics automation systems, and a global delivery service system.
Jiang Peiliang pointed out that formation and grading is one of the most energy-consuming steps in the lithium battery production line. Currently, there are three major challenges in the grading process: first, the accuracy of capacity testing is low due to the effects of low current precision, poor uniform temperature characteristics of storage locations, and large capacity margin of battery cells; second, high construction costs of production lines due to the difficulty in factory design and construction, long construction periods, and low commissioning efficiency; third, high factory production energy consumption caused by problems such as low efficiency of individual machines, high power consumption of factory fans, and high equipment failure rates.
ZhiJiaNeng focuses on the complete solution for lithium battery post-processing formation and grading, introducing the third-generation gallium nitride grading water-cooled integrated machine. The power module uses the third-generation semiconductor material gallium nitride, precisely controlling the current and voltage accuracy to ±0.025%FS+±0.025%RD, with 5-bridge arm phase-shifting output, and current ripple error less than ±0.05%FS (within ±200mA); water-cooled internal circulation cooling ±2°C, maintaining a constant battery charging and discharging temperature environment, significantly improving battery cell yield and capacity calculation consistency.
Compared to traditional solutions, ZhiJiaNeng’s post-processing formation and grading complete line solution effectively reduces construction costs by 15%-20%, saves 30% of site occupancy area, shortens the commissioning period by 67%, and reduces factory production energy consumption by 20%.
Among them, the gallium nitride power module combined with 700V DC bus technology greatly improves charging and discharging efficiency; the energy consumed in a full capacity charge and discharge cycle accounts for only 37% of the total battery energy, which is 60% lower than traditional solutions, and reduces distribution capacity by 10%.
Compared to traditional separate solutions, the system operation cost is reduced by 25%. Taking the construction of a single production line by a battery cell factory as an example, it can save the company 11.43 million kWh of electricity per year. Calculated at a price of 0.7 yuan per kWh, it saves about 8 million yuan in costs annually and reduces carbon dioxide emissions by more than 10,000 tons.
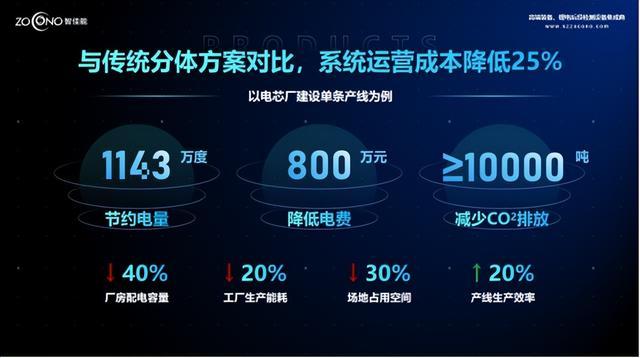
At the same time, matched with ZhiJiaNeng’s independently developed formation and grading software system, it can help the end-users operate more efficiently and stably.
From reducing the cost of equipment, construction to operation, ZhiJiaNeng’s lithium battery post-processing formation and grading complete line solution has achieved industry-leading status.
Warehouse Logistics Full-Line Automation System: Self-Developed and Produced Equipment Rate Reaches 85%
ZhiJiaNeng’s lithium battery warehouse logistics full-line automation system has years of cooperation experience with leading industry customers. In terms of full-line solutions, core single-machine equipment, and intelligent software systems, ZhiJiaNeng’s rate of self-developed and produced equipment holds a leading position in the industry.
It is reported that ZhiJiaNeng’s warehouse logistics division’s cooperative customers basically cover the top enterprises in the lithium battery industry as well as companies with broad prospects in niche markets, including CATL, BYD, LG, Zhongchuang Xinhang, RuiPuLanJun, Honeycomb Energy, EVE Energy, Choneng New Energy, Penghui Energy, Zhenli New Energy, Xingwangda, Lishen Battery, and so on.
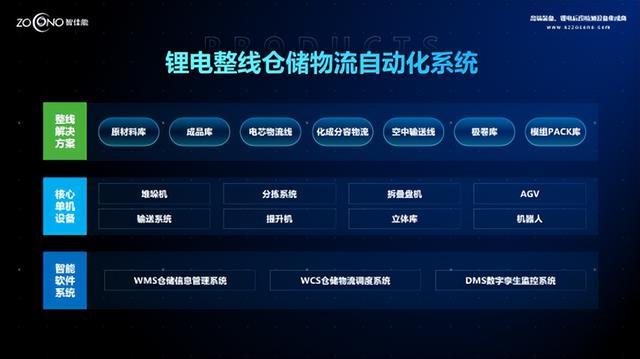
Jiang Peiliang stated that in the past few years of lithium battery expansion, the warehousing and logistics segment has faced three major pain points: instability throughout the delivery process, operational results falling short of expectations, and insufficiently rapid response services.
In response, ZhiJiaNeng, with 85% of its equipment independently developed and produced, achieves high-quality delivery and operation. Currently, the company has delivered over 2,000 stacker cranes, more than 1,000 elevators, over 200,000 meters of conveyor lines, more than 3 million storage locations, over 400 shuttle cars, and more than 600 AGVs, among others.
Solid data also confirms that ZhiJiaNeng’s warehousing and logistics full-line solutions have gained increasing recognition from more customers at the terminal.
In terms of software, ZhiJiaNeng also possesses a robust software R&D technology platform, offering customers full-process customized services. The company has independently developed the WMS Warehouse Information Management System, WCS Warehouse Logistics Scheduling System, and DMS Digital Twin Monitoring System.
These systems can meet the needs for pre-commissioning, completing 90% of business and high-load testing on-site; flexible customized development, with fully configurable product interfaces; visual editing of monitoring layouts, and customized development of digital twin 3D monitoring services.
ZhiJiaNeng’s ability to stand out in the competitive post-processing equipment market is inseparably linked to its profound technical expertise, high self-development and production supply rate, continuous product innovation and iteration, guarantee of efficient and high-quality delivery, and rapid after-sales response.
Indeed, facing the long-term development of new energy, equipment companies can only possess strong and enduring leadership by mastering core technologies and differentiated competitive advantages.
Expanding Overseas “Friend Circle” and Accelerating Global Reach
Currently, with the rapid growth of the global new energy market, Chinese companies face multiple challenges in going global, such as geopolitical and cultural differences, local laws and regulations overseas, challenges in overseas supply chain management, high labor costs, technical barriers, and the dilemma of talent going abroad.
Jiang Peiliang stated that ZhiJiaNeng relies on the integration of advantageous resources to continuously expand its overseas “friend circle.” The company has signed a strategic cooperation agreement with Huawei Digital Energy, allowing shared access to Huawei’s local service teams overseas. This greatly solves the challenges encountered by non-core technologies abroad and quickly establishes an overseas delivery advantage.
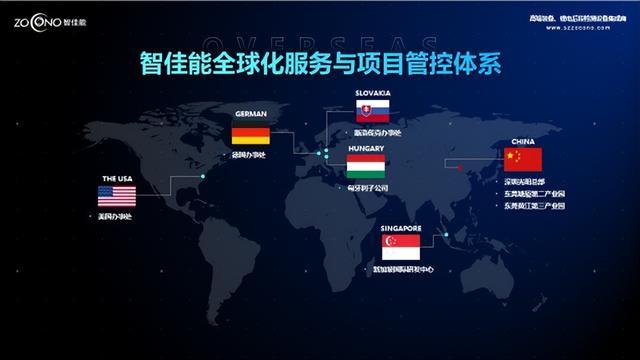
At present, ZhiJiaNeng has established a wholly-owned subsidiary in Hungary, an international R&D center in Singapore, and offices in the United States, Germany, and Slovakia. Combined with three major production bases in China, ZhiJiaNeng’s global service and project management system has taken shape. Additionally, the company has cooperated and exchanged with the Ministry of Commerce of China and the energy departments of multiple countries overseas, continuously strengthening scientific and technological innovation cooperation with “Belt and Road” countries, laying a solid foundation for the future overseas product delivery and localized manufacturing of ZhiJiaNeng.
Jiang Peiliang finally emphasized that ZhiJiaNeng is always grateful for the trust and support given by downstream customers and upstream suppliers. The company also hopes to move forward with the industry, traverse cycles together, and grow resiliently.