Solid-State Batteries: Beyond Material Systems
Dr. Li Zheng, General Manager of SAIC Qingtao, presented a contrasting viewpoint at the 2023 Advanced Lithium Battery Annual Conference in November, challenging the previous industry consensus.
For a long time, solid-state batteries have been regarded as an ideal solution to address safety concerns and enhance energy density in lithium-ion batteries. Initially, the development of solid-state batteries involved stacking materials, selecting the highest capacity positive and negative electrode materials in the industry, and replacing the separator and electrolyte with a solid-state electrolyte.
Especially in 2023, with battery homogeneity facing serious overcapacity and power battery technology reaching a critical point of comprehensive upgrade, solid-state batteries for vehicles and continuous capacity planning have been frequently discussed, generating high market expectations.
However, it is important to exercise caution regarding the risk of excessive industry expectations.
Li Zheng pointed out that there is still a misconception about solid-state batteries in the industry, and understanding them solely from a material perspective is incomplete. He stated, “The industrialization of solid-state batteries involves a comprehensive upgrade from material systems to battery structures to process technology.”
Currently, the material system for solid-state batteries has not yet been established, and the production line equipment is not fully equipped, resulting in a chaotic state within the solid-state battery industry chain.
Considering the market, the focus of the electrification market for solid-state batteries has shifted from front-end technology layout to products that are on the verge of application. In light of this contextual change, reevaluating solid-state batteries becomes the first step in adjusting industry strategies.
Reassessing Solid-State Batteries
Li Zheng emphasized that solid-state batteries offer a solution to the limitations of the solid-liquid material system.
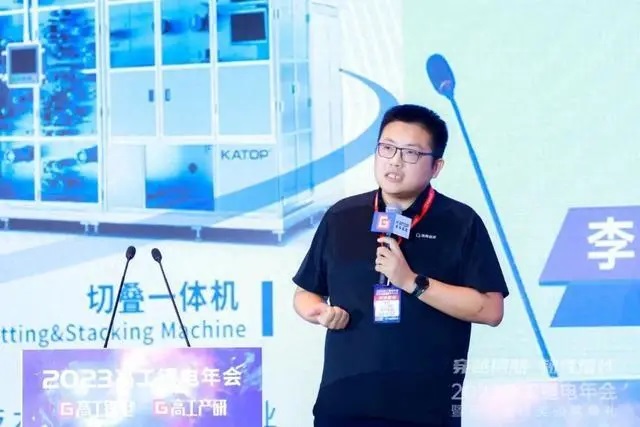
When we look at the development of liquid batteries, the electrolyte system based on solvents like PC, EC, and DMC has been in use since the early stages of commercialization. Throughout this process, battery performance has steadily improved, with cycle life increasing from an initial 50 cycles to tens of thousands of cycles. Additives have been continuously incorporated into the electrolyte, and both positive and negative electrode materials have undergone surface treatments to stabilize the solid-liquid interface.
Overall, the development of the solid-liquid battery system has followed an additive approach. However, this development logic has also imposed constraints on the application of battery materials. If we can break away from the “fixed pattern” of high-nickel ternary positive electrodes paired with silicon-based/lithium metal negative electrodes, the comprehensive upgrade of solid-state batteries holds immense potential.
Li Zheng stated that the advantages of solid-state batteries lie in the absence of a liquid system. This allows positive electrode materials to extend beyond the 4.2V platform, and high-manganese materials can be utilized without concerns of manganese dissolution. Additionally, the process reduces steps, simplifying the overall process and promoting energy efficiency.
Interface Challenges and Industry Chain Gaps
The potential of solid-state batteries is accompanied by challenges in core technology and supporting industry development.
The issue of solid-solid interfaces poses a significant hurdle on the path to industrialization. These interfaces involve both physical and chemical contacts, and finding the right balance between electrical conductivity, reducing side reactions, and lowering impedance remains a key focus for the industry.
Various solutions are being explored commercially, leading to the emergence of different technical routes for solid-state electrolytes. Li Zheng suggests paying attention to the chloride route in addition to the sulfide route, as it offers low cost and excellent process compatibility.
Closing the gaps in the industry chain and advancing technological breakthroughs must progress hand in hand. Dr. Li Zheng highlights the current lack of momentum, materials, and process technology in the solid-state battery industry chain.
Automakers lack sufficient motivation to develop solid-state batteries due to a widespread misconception. Solid-state batteries are still not considered outstanding in terms of cost and performance compared to conventional lithium-ion batteries for automotive applications.
The new material industry scale in the solid-state battery system is small, and the supply of high-manganese positive electrodes and solid-state electrolytes does not meet demand. Progress in the development of lithium-containing negative electrodes is also slow.
Process technology development lags behind the changes in the new material system of solid-state batteries. Innovative processes, such as dry positive electrodes, do not yet meet production requirements.
As the industrial development of solid-state batteries progresses, the degree of iteration and renewal of production lines will increase steadily, leading to a gradual decrease in battery costs.
In the semi-solid state stage, 30% of production line equipment will be innovated, making costs comparable to
Solid-State Batteries in the Context of Comp
The market is seeking the next generation of power batteries to meet the broader goal of comprehensive electrification. This goal extends beyond promoting the market penetration of electric vehicles and encompasses electrification in various domains, including land, sea, and air.
What new requirements does the era of comprehensive electrification pose for power batteries? Li Zheng believes that in this era, winners are not those with a single technology that is “far ahead,” but rather those who are “all-around champions” and “polygon warriors.”
SAIC Group’s internal battery evaluation system includes over 20 indicators, but they can be summarized into core aspects such as cost, safety, performance, and durability.
SAIC Qingtao’s focus on its own solid-state battery will also revolve around promoting comprehensive development in eight dimensions: cell cost, thermal stability, energy density, consistency, charging performance, low-temperature performance, cycle life, and calendar life. Battery products evolving from liquid to semi-solid to full solid-state will gradually meet various ideal indicators in the market.
Dr. Zhang Xiaofei, Chairman of Advanced Lithium Battery, points out that the current market tendency to prioritize cost in battery product development should be approached with caution. It is necessary to avoid ineffective investment in low-end capacity and instead focus on developing next-generation battery technologies, including solid-state batteries and dry electrode technologies, to shift the industry from rolling to expanding.